From planting to harvest, the benefits of precision technology can really add up, says no-tiller Tim Norris of Gambier, Ohio. The Ohio Master Farmer previously owned Ag Info Tech, a precision agriculture company, serving over 800 different farms in Ohio and Pennsylvania.
When Norris looks at tech for a planter or sprayer, he sees more than a costly instrument — he sees payoffs on the bottom line.
“Precision ag is one of the keys to our farm's success,” Norris says. “We really don't have as productive soils as the farmers to the west of us. We also don't have the efficiency of scale like a lot of larger farms do, so we need to be as efficient as possible with our inputs.”
.jpg?1723049123)
No-Tiller Tim Norris of Gambier, Ohio, plans his seed rates based on and the area of the field. He and his agronomist then create a map like this one with four zones with varying rates of seed for each zone.
Relieving Stress on the Bottom Line
That input efficiency is made possible by precision agriculture tools. Using the 4Rs — defined as placing the right product in the right place at the right rate at the right time — is a stress reliever, Norris says.
“By using precision soil sampling and variable rate application (VRA) lime and fertilizer, you will always know what every area of your field needs,” Norris says. “You will never have to question your fertilizer and lime programs.”
In an Ag Info Tech study of 77,000 acres, using VRA lime saved $21.90 per acre, VRA phosphate saved $12.90 per acre, and VRA potash saved $5.94 per acre. Combined, VRA saved $40.74 per acre total. Subtract the cost of precision soil sampling at $12 per acre, and the VRA return on investment (ROI) per acre is $28.74. Norris notes that these numbers don’t account for yield gain that results from placing more fertilizer in low fertility areas, which would also contribute to increased ROI.
Steering Systems Reduce Overlap
Ag Leader’s SteadySteer, John Deere’s AutoTrac Universal 300 and Raven Industries’ DirecSteer are examples of assisted steering systems. These systems attach to the steering wheel to turn it, reducing operator fatigue. Norris says the system, combined with the free Wide Area Augmentation System (WAAS) signal, can also reduce overlap and inputs.
“Assisted steering can steer you through the field within 6-8 inches of where you need to be 95% of the time,” Norris says. “By reducing that overlap period, gaining extra time and speed, and working a little later at night, you can get about 10% more done per day.”
For a $9,000 assisted steering system, it only takes 1,108 acres before seeing ROI, according to Norris. He says by reducing the number of overlapped acres by 7%, there also is a 7% reduction in the amount of labor, fertilizer and herbicide used.
Autosteer, which is integrated into new equipment, can eliminate overlap, too. Norris uses a free signal from the Ohio Department of Transportation.
“Real Time Kinematic (RTK) auto-steer will steer you through the field within 1 inch of where you need to be 95% of the time,” Norris says.
Norris estimates that an RTK auto-steer system costs $18,000-$25,000. With this system, there are 3% fewer acres to plant, which translates to 3% less seed, labor and fertilizer used. For a system that costs $18,000, it would take 3,333 acres to see ROI, while a $25,000 system would take 4,629 acres to see ROI.
Norris says dealing with corn stubble was one of his first challenges with auto-steer in no-till soybeans. Rotary mowing and vertical tillage left the corn stalks susceptible to wind and water loss.
“RTK guidance was our answer,” Norris says. “When we planted corn with a 12-row planter and the soybeans with the same planter, only as a 12/23 row, it worked well. That worked really well until we got a 16-row corn planter. When we were doing a 12/23, and we planted the corn and beans with the same planter, if we were on the side of a hill, the planter drifted the same amount the next year, but then the following year, it drifted a lot more. Now, our best option is to keep the planter in great condition and plant on a slight angle.”
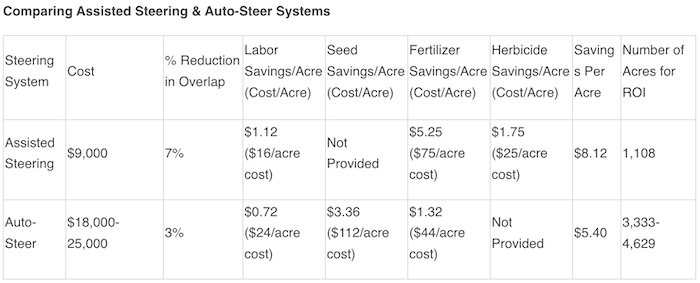
Table 1. Comparing assisted steering to auto-steer shows large differences in areas such as overall cost, labor savings, fertilizer savings and more.
Table 1. Comparing assisted steering to auto-steer shows large differences in areas such as overall cost, labor savings, fertilizer savings and more.
Precision and Greater Yields
Norris says planter performance monitoring solutions, like variable rate population control, can increase yields at harvest.
“Planter performance monitoring solutions give you a virtual look at how your planter is performing,” Norris says. “It allows you to see problems with your seed meters while planting so you can make the necessary corrections.”
For example, advanced seed monitoring can identify problem areas like plugged holes on a seed disk. Norris says that fixing one row with a skip because of a plugged hole on a seed disk would yield 1 bushel more per acre. Assuming the cost to fit the advanced seed monitoring system on a 16-row planter is $2,000 and the price of corn is $4.20 per bushel, Norris says only 476 acres need to be planted before the technology pays off.
Another planting tool is variable rate seeding, allowing the user to plant corn in higher populations in areas that need more seeds. It also plants less seed in areas of the field that don’t benefit from lots of planting.
.jpg?1723049564)
Curve compensation, which enables planting a consistent seed population, is a main benefit of electric drives. This technology also provides many of the same benefits as row shutoffs and variable rate applications.
With a 4-bushel per acre yield increase, Norris says only 714 acres need to be planted in order to see a return on investment for the variable rate seeding technology.
Individual row shutoff saves 4-5% on seed by preventing seed flow when the planter reaches an area that has already been planted. As a result, headlands and point rows will not be double planted, and yields should increase because the rows are not overpopulated.
Norris says the typical yield loss in areas that are double planted is 20%. He says there is a 4% savings on a $280 bag of seed with a population of 34,000, plus a 20% yield increase on the 4% of the crop that had previously been double planted.
Hydraulic downforce keeps the gauge wheel in contact with the ground by automatically adjusting downforce. This system does this without compacting the soil.
“This makes your planter unit ride much smoother resulting in more even stands,” Norris says. “The Beck’s Hybrids test plot results show an average yield increase of 11 bushels per acre when using hydraulic downforce vs. down-pressure springs. An on-farm research study showed an average of 1,500 extra ears per acre using hydraulic downforce.”
Planter Performance Monitoring Solutions
Planter Performance Monitoring Solution |
Cost to Fit on 16-row planter |
Yield Increase Per Acre |
Profit Per Acre, Assuming $4.20/Bushel Corn |
Number of Acres for ROI |
Advanced Seed Monitoring |
$2,000 |
1 bushel |
$4.20 |
476 |
Variable Rate Seeding |
$12,000 |
4 bushels |
$16.80 |
714 |
Individual Row Shutoffs |
$14,000 |
1.4 bushels |
$5.88 |
1,315 |
Hydraulic Downforce Control |
$36,000 |
11 bushels |
$46.20 |
779 |
Table 2. Comparing different planter performance monitoring solutions shows hydraulic downforce control solutions cost by far the most to fit but brings the highest yield and profit per acre.
Technology Stacks Add Up
“The real benefit is using these technologies together as these systems can be built upon,” Norris says.
For example, if Norris combines variable rate application with a profit of $28.74 per acre, RTK auto-steer with a profit of $5.40 per acre, advanced seed monitoring with a profit of $4.20 per acre, row shutoff with a profit of $5.88 per acre and hydraulic downforce control with a savings of $46.20 per acre, he would have a total revenue increase of $90.42 per acre.
The complete system would cost $65,000 for a Kinze 16-row planter and New Holland tractor.
“The system would pay for itself in 2 years on 400 acres of corn,” Norris says.
He says that these technologies aren’t the only ones available. There are other solutions that can be stacked to create the ideal precision ag technology solution for each individual farm.
Related Content
Use Precision Data to Create Profit Maps for Your No-Till Fields
No-Tiller Calculates $8 Per Acre Loss By Going 1 Mile Slower at Harvest
[Podcast] Realizing ROI and Identifying Pain Points of Precision Tools Part 1